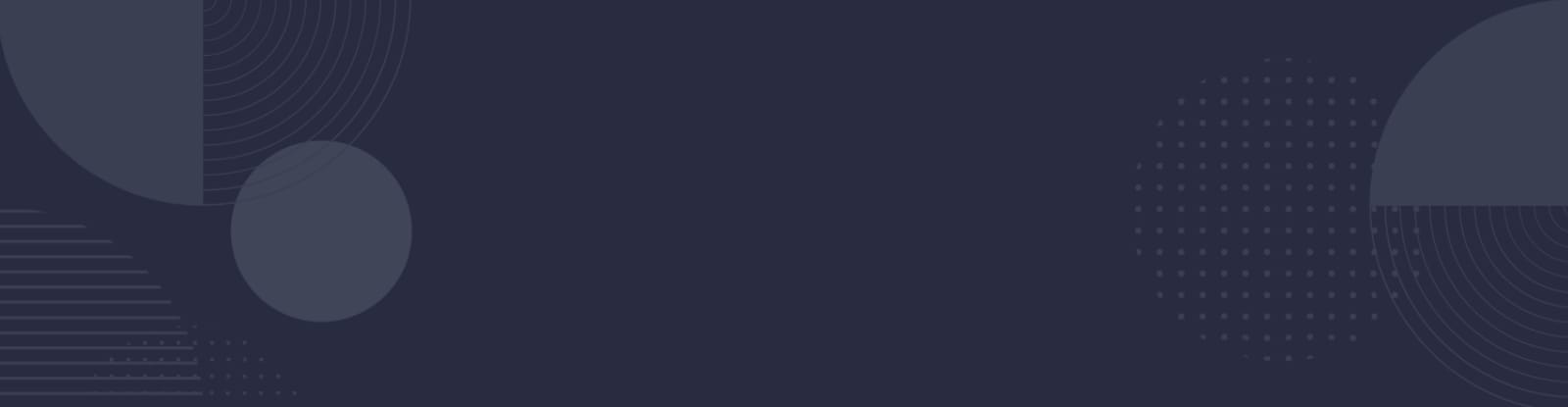
Lamination Guide
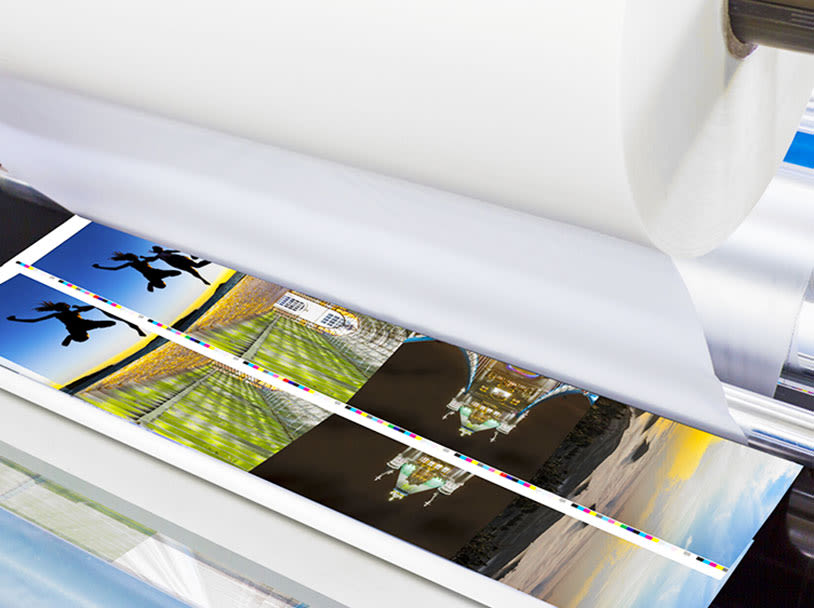
Lamination
Lamination is a very simple process that can enhance the appearance of and strengthen any document in just a few minutes. For this reason, laminators have become increasingly popular: in the office for important documents, at home or in a professional context for photographic prints, in publishing for book production, and to protect and enhance posters, panels and advertising posters. This guide is intended to help you understand the differences between the various existing laminator models, the available functions and possible uses so that you can choose your next laminator with ease and confidence.
What to laminate?
Laminating can be used for a wide range of purposes, both at home and at work:
At home it can be worthwhile laminating: photos and collages of photos, personalised calendars, children’s work and drawings, greeting cards and invitations, personalised bookmarks, passes and cards to be kept in your wallet, luggage labels, school, gym or train timetables, recipes.
At work lamination can serve not only to preserve over time, but also to give an improved and more formal appearance to: price lists, catalogues and brochures, presentations, promotional material, business cards, badges and ID cards, membership cards, phone books.
Why laminate?
Laminating is a quick and convenient way to preserve documents. Applying a thin film can protect any type of sheet, making it durable and protecting it from scratches and external factors such as water, weathering and UV rays.
The lamination process consists of gluing a gloss or matt film to one or both surfaces to be laminated. Gloss film makes text sharper and enhances colours and images; matt film makes text more legible by preventing glare on the sheet.
The benefits of lamination:
It makes work documents and presentations look more professional;
It preserves documents or photos from the effects of time or weathering due to water or sunlight;
It protects documents against forgery;
It allows you to make posters, signs or badges yourself;
It improves the aesthetic appearance of products by making colours and images brighter;
It eliminates creases and wrinkles for a perfect finish.
How to choose a laminator?
When addressing the need to purchase a laminator, you need to assess multiple factors to choose the product that best suits your needs. Let’s look at them in detail.
Laminator types
Laminators can use two different lamination technologies: hot or cold.
Hot laminators are generally the most popular. The lamination process in these machines is very simple: once the laminator has heated up, just insert the pouch or sheet covered in plastic film into the laminator. Its internal rollers will take the document through a “hot zone”, which has been heated to the most suitable temperature for the plastic being used. This will result in a waterproof plastic-coated sheet with an excellent appearance, which withstands the effects of time and wear.
Cold laminators, on the other hand, use plastic film with one adhesive side and operate as follows: the sheet to be laminated passes between two adhesive films followed by two or four rollers, which are suitably adjusted to make the two adhesive films stick to the two faces of the paper or card sheet. The result is usually excellent and air bubbles are rarely trapped between the sheet and plastic film. The cold lamination process is generally used when the document to be laminated could be damaged by heat. Cold laminators are often considered safer than hot laminators, but generally result in a product with a shorter life span.
Cold lamination is mainly used for large sizes and signs, while hot lamination is more suitable for small sizes.
For both types of lamination, it is important to ensure that the sheets to be laminated are perfectly clean and free from dust or other particles as they will be visible and may create unaesthetic bumps on the laminated surface after lamination.
Document sizes
The sheet size supported by a laminator varies with the model. Therefore, when purchasing a laminator, make sure that it can meet all your laminating needs.
Thickness
The unit usually used to express the thickness of the pouch of adhesive film is the micron, which is one thousandth of a millimetre. When the features of a laminator include that it supports thicknesses up to 200 microns, it means that the machine can laminate sheets using film with a maximum thickness of 0.2 mm. The film thickness also varies with the machine model.
Speed
Some laminators can laminate sheets faster than others. Sometimes, however, a higher lamination speed means the resulting sheet has a lower quality. Many laminators let the user choose the laminating speed, to adapt the machine to any specific use.
Pouch or roll laminators
Pouch laminators are the most common type among office laminators. The small size of these machines means they can be moved easily from one desk to another, and kept in drawers or cabinets. They usually contain 2 to 6 rollers to make the pouch adhere to the sheet being laminated. The more rollers there are, the more evenly the heat will spread, resulting in higher lamination quality.
Tosingraf offers a wide range of easy-to-use and highly reliable pouch laminators. All of the machines can laminate without the use of protective card (carrier) and using pouches of all existing thickness. They can also process foils (special coloured sheets), which transfer colour to the inserted document when heated by the machine.
Film roll laminators are usually used in print centres. Tosingraf offers innovative laminators that can conveniently laminate large quantities of documents, even large ones, with high production rates. An adhesive film laminator produces a professional-looking sheet that is protected against staining and creasing.
Pouches and adhesive film: how to choose them
To ensure that laminators work properly, it is important to know how to purchase the right consumables as well. You need to find out which type of consumable is compatible with your laminator model.
Pouches
Pouches are plastic “pockets” that are open on three sides, into which the sheet to be laminated is inserted. They may be gloss or matt, depending on taste, and are usually used in hot laminators.
Size and thickness are characteristics to consider before purchasing pouches. They must be of the most suitable size for the document to be laminated and of a thickness supported by the laminator purchased. Tosingraf offers many pouch sizes and thicknesses, from standard to custom.
It should also be noted that the pouches are slightly larger than the normal sheet sizes since they are made to cover the entire sheet and insulate it from external agents (the edges of the sheet must also be well protected).
Adhesive film
Adhesive films for laminators come in rolls and are used to laminate large documents.
The definition hot film or cold film does not refer to the film itself, but to the glue used to make it adhere to the surface on which it is applied. Hot glue is very suitable for paper surfaces because it penetrates the fibres, ensuring a high level of adhesion while remaining very clear. Cold glue, on the other hand, adheres very well to synthetic materials that are not porous.
Tosingraf adhesive films are available in various thicknesses and sizes and have been designed to ensure optimal lamination in every application.
Frequently asked questions
How can I prevent dust from forming between the sheet and the adhesive film?
It is good practice to avoid leaving the adhesive film or pouches unattended after they have been unpacked. To prevent dust from forming and lowering the lamination quality, it is advisable to clean the sheets to be laminated before inserting them into the machine.
How can I prevent air bubbles from forming during lamination?
The formation of small, tiresome air bubbles in the laminated document greatly affects its quality and appearance, but this problem can be eliminated. This effect is the result of the laminator being too hot: the heat risks melting the film and glue too much, causing small bubbles to form. To avoid this unfortunate issue, it is advisable to set the laminator to the most suitable temperature.
How do I prevent the laminated document from appearing opaque?
The lamination may be opaque because the laminator temperature is too low. This occurs because the glue on the adhesive film or pouch does not melt properly and does not adhere to the document perfectly. To solve this issue, pass the same document through the laminator twice, or raise the laminator temperature. The thicker the adhesive sheet, the higher the temperature needs to be.
UV coating
A UV coating acts as a seal, and serves to protect the printed product while enhancing it aesthetically. It is a colourless, water-based acrylic coating that hardens and dries very quickly under the action of UV rays. A UV coated product is exceptionally glossy and resistant to abrasion and heavy mechanical stress. The drying process improves and optimises the properties of the product, protecting it from abrasion and making it water-repellent.
Applying a UV coating to the covers of brochures and catalogues or to the surfaces of postcards, business cards, posters and flyers produces high-quality products to offer the market. UV coating is a valid alternative to gloss lamination. It offers higher and more refined quality, but is less cost-effective.
When to choose UV coating: for example, leaflets or folding flyers containing price lists, calendars, or overviews of scheduled events pass through the hands of many people, and must be made with a durable, strong print finish such as UV coating to withstand the effects of time and wear. These products are subjected to the greatest “stress”, and must therefore be protected with greater attention.
The UV coating machine is fully enclosed, with a manual infeed table. The liquid coating is applied at the infeed, and falls in the middle between two rollers and spreads out over the whole surface. The excess liquid is collected in a tray underneath and is returned to the initial stage. A conveyor belt runs inside the machine, passing through the heated area to fix the liquid with UV lamps.
Resin coating
Resin coating is a surface treatment that serves to protect stickers, labels and gadgets, and give them a long-lasting three-dimensional (3D) effect.
The transparent dome applied over the design creates a lenticular vision that enhances the graphics and colours while protecting them from the effects of weather and abrasion. The result is a unique product, a combination of technology and aesthetics.
Benefits of resin coating: a resin-coated sticker can add value to any product making it more precious. It also makes the sticker easier to read, so resin-coated stickers are also known as lenticular: in fact, the resin coating functions as a magnifying glass. The resin coating increases resistance to weather, UV rays and abrasion.
Products that can be made: 3D-effect stickers, key fobs, pens, signs, cuff-links, badges, stickers for decorating furniture and appliances, promotional items, card decorations, trophies and medals.
Resin coating is done with a polyurethane resin: a clear, soft, flexible resin that does not yellow.